When it comes to epoxy flooring, one of the most critical decisions you’ll make is how thick your coating should be. The right thickness not only ensures the longevity and performance of your floor but also optimises cost and appearance.
To make an informed choice, you must first understand the factors that determine the right epoxy floor thickness. This is how you’ll avoid costly mistakes down the track, whether you’re installing a light-duty residential garage floor or a heavy-duty industrial workshop.
Why Epoxy Floor Thickness Matters
An epoxy floor’s thickness determines its mechanical strength, wear resistance, and ability to withstand impacts, chemicals, and abrasion. Too thin a coating may peel, crack, or wear through prematurely, leading to maintenance headaches and potential safety hazards.
Conversely, an overly thick system can be unnecessarily expensive, may take longer to cure. It could also trap solvents, leading to surface “bubbling.”
By selecting the correct thickness for your application, you’ll find a balance between performance, durability, and cost-effectiveness. You’ll maximise your return on investment for any property development or space renovation.
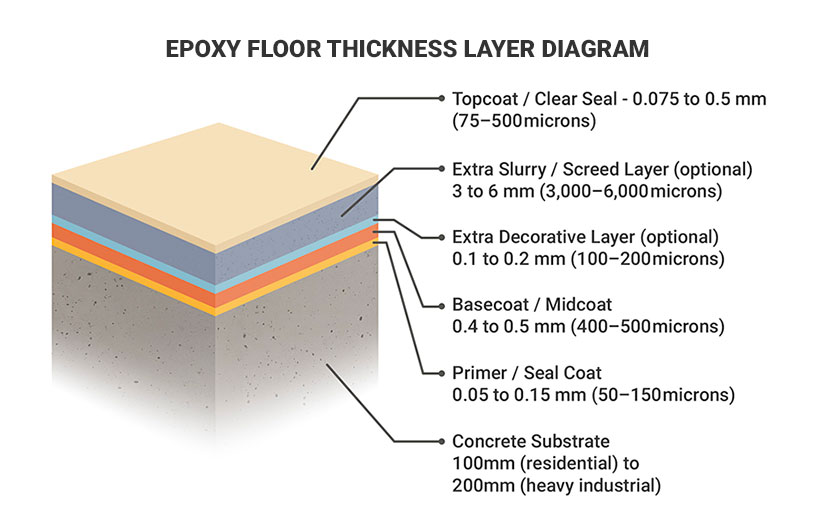
Key Factors Influencing Epoxy Floor Thickness
- Substrate Condition
- Surface Profile & Porosity: Rough or porous concrete can absorb epoxy, effectively reducing the thickness of the applied film. High spots may receive a thinner coat, while low spots puddle excess material.
- Levelness: Floors with significant undulations may require thicker build-up or a separate self-levelling underlay before applying the main epoxy layer.
- Traffic & Load Requirements
- Pedestrian Traffic: Light residential use, such as foot traffic or light trolleys, often performs well with thinner epoxy films (100–200 microns).
- Vehicular Traffic: Garages, showrooms, and car parks require at least 300–500 microns to resist tyre scuffing and minor oil spills.
- Heavy Machinery & Forklifts: Warehouses, manufacturing plants, and workshops may need 1–3 mm (1,000–3,000 microns) or more, often combining epoxy resin with quartz or polymer aggregates for additional strength.
- Chemical & Impact Resistance
- Chemical Exposure: Laboratories, food processing areas, and chemical plants demand thicker, chemical-resistant formulations, typically at least 500 microns, plus specialized epoxy chemistries.
- Impact & Abrasion: Loading docks and high-drop zones benefit from epoxy screed systems of 3–8 mm to dissipate impact forces and guard against surface fracture.
- Aesthetic & Functional Requirements
- Decorative Finishes: Metallic or decorative flake systems may call for multiple coats (primer, base, flake, and clear seal), totalling 300–600 microns.
- Slip Resistance: When embedding anti-slip additives, you may need an extra 100–200 microns overlay to encapsulate the grit uniformly.
Typical Epoxy Floor Thickness Ranges & Applications
Thickness | Typical Use Cases | Notes |
---|---|---|
Below 250 microns | Light residential: utility rooms, light storage | Primer + single coat |
250–500 microns | Garages, showrooms, moderate commercial areas and other moderate utility applications | Primer + topcoat; basic flake or colour broadcasts |
1–3 mm (1,000-3,000 microns) | Industrial workshops, food processing, labs | Self-levelling systems with quartz aggregate |
3–8 mm (3,000-8,000 microns) | Heavy-duty screed floors, loading docks, extreme or specialty chemical labs | Multi-layer build-up; very high impact and abrasion zones |
Step-by-Step Guide to Selecting the Right Thickness
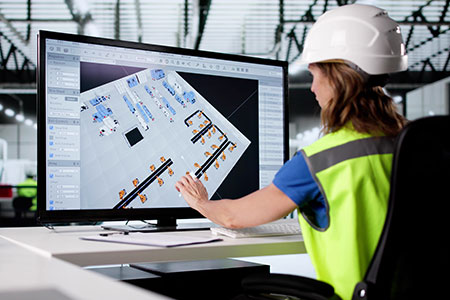
Step 1. Assess Your Concrete Substrate
Before specifying epoxy, conduct a full Concrete Floor Preparation inspection. Check for cracks, moisture ingress, and surface profile. Proper diamond grinding or shot-blasting will both improve adhesion and reduce the amount of epoxy absorbed into the slab.
Step 2. Define Your Traffic & Load Profile
Make a list of all expected loads, such as foot traffic, vehicle weights, forklift operations, trolleys. Then classify them as light, medium, or heavy. Use this profile to match the appropriate thickness range above.
Step. 3 Consider Environmental & Chemical Exposures
Identify any chemicals (acids, alkalis, oils) that the floor will face. If you’re unsure whether standard epoxy will suffice, opt for a thicker, chemical-resistant formulation or high-build screed.
Step 4. Factor in Maintenance & Lifecycle Costs
Thicker floors often last longer and require fewer repairs, but upfront costs rise. Balance the initial investment against downtime and repair expenses over the floor’s expected lifespan.
Step 5. Consult with Epoxy Flooring Specialists
Every project is unique. Our team at Art of Concrete Epoxy Flooring Perth can perform a site audit, recommend the optimal thickness, and provide a transparent quote. We’ll also advise on whether a multi-coat decorative finish or a heavy-duty screed system best suits your needs.
Integrating Epoxy with Polished Concrete & Other Finishes
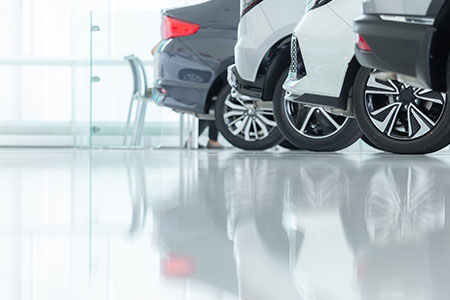
If you’re still weighing up epoxy versus polished concrete, check our in-depth comparison in “Polished Concrete vs Epoxy” to understand the pros and cons of each system:
Polished Concrete vs Epoxy
In some spaces, a hybrid solution—polished concrete substrate with epoxy or polyaspartic topcoat (a fast-curing aliphatic polyurea)—delivers the best of both worlds: aesthetic elegance and high-performance protection.
Professional Installation & Maintenance
No matter how well you choose your epoxy thickness, proper application is key. Our certified installers follow a stringent 5-step process:
- Site Inspection & Preparation – Grinding, crack repair, moisture testing
- Primer Application – Seals pores, improves adhesion
- Basecoat & Build-Up – Applied to specified thickness, with aggregates if needed
- Decorative/Topcoat – Colour broadcast, flakes, or metallic finishes, plus sealer
- Curing & Quality Check – Ensuring full cure before load-in
Routine maintenance (sweeping, damp mopping, and periodic deep cleaning) will also extend the life of your floor. For heavy-use sites, schedule annual inspections to check for wear and consider touch-up coats in high-traffic zones.
Conclusion & Next Steps
Choosing the correct epoxy floor thickness isn’t just about pouring more material. It’s about matching your concrete substrate, traffic requirements, environmental exposures, and aesthetic goals.
By following the steps outlined above and partnering with experienced professionals, you’ll ensure a durable, cost-effective floor finish that enhances safety and looks great for years to come.
Ready to specify the perfect system for your space? Contact our team today for a free site audit and tailored recommendation: Art of Concrete Epoxy Flooring Perth.
Do you have questions about concrete preparation or want to explore other flooring options? Begin here:
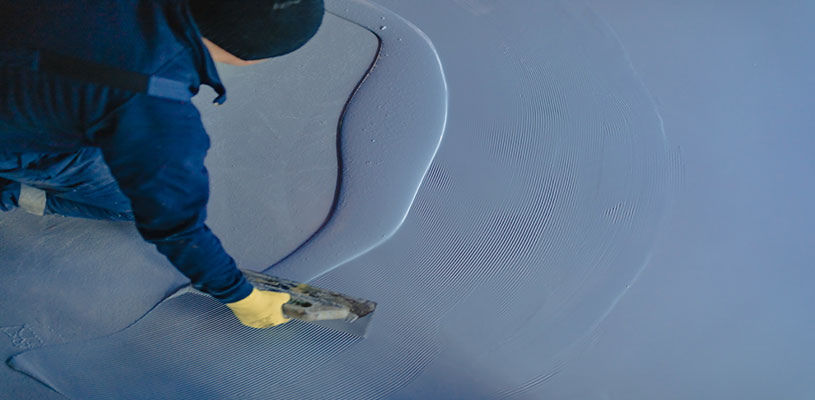